Металлокерамика с уступом
Металлокерамика совершила настоящий эстетический прорыв в современной стоматологии. Интересен тот факт, что словом «металлокерамика» называют не только материал, из которого изготавливаются коронки, но и методику замещения дефектов с помощью этих протезов. Такие конструкции применяются в том случае, когда зуб разрушен и не подлежит восстановлению с помощью иных материалов. Металлокерамика дает возможность изменить форму и размер коронки зуба, ее цвет и даже расположение в зубном ряду.
Металлокерамическая коронка представляет собой тонкостенный металлический колпачок, который покрывают керамической глазурью. Лучшими материалами для изготовления металлической основы коронки являются благородные металлы (золото, платина) и титан. Снаружи каркаса наносится керамическая масса и закрепляется путем спекания. В результате коронка выглядит как здоровый зуб.
Точность передачи цвета зависит от качества керамической массы.
Для выбора цвета коронки пользуются специальными палитрами. Они представляют собой набор тонких фарфоровых пластинок разных цветов и оттенков. Мировыми лидерами на рынке производства керамики являются фирмы «Ivoclar», «Ducera», VITA. При выборе фарфора важными показателями являются его прочность и коэффициент теплового расширения. Прочность должна быть не ниже 50 Мпа. Коэффициент термического расширения не должен изменяться при многократных обжигах.
Этапы изготовления металлокерамической коронки:
- Препарирование зуба под металлокерамическую коронку.
Производится снятие твердых тканей зуба на толщину коронки, которая составляет 1,5 мм. Рекомендуется создавать уступ в пришеечной области, во избежание образования синей каймы вдоль шейки коронки. Уступ представляет собой узкую площадку вдоль шейки зуба шириной 0,5-2 мм. Препаровка с уступом достаточно трудоемкая, она требует наличия современной стоматологической установки и высокой квалификации врача-ортопеда. Депульпировать зубы под металлокерамику целесообразно только при наличии в них воспалительного процесса, так как зуб после удаления нерва становится более хрупким.
- Снятие двухслойного оттиска. Для более точного отображения всех деталей зуба десна отодвигается с помощью специальной ретракционной нити.
- Далее в лаборатории по оттискам из гипса изготавливается модель, на которой создается будущая коронка из воска. По гипсовой модели отливается металлический каркас. На отпрепарированные под керамику зубы на время изготовления протеза одеваются временные коронки, которые защищают зуб от раздражающих воздействий и уменьшают психологический дискомфорт.
- Проверка каркаса в полости рта и определение цвета будущей коронки с помощью специальных палитр.
- Протез снова передается в лабораторию, где начинается нанесение фарфоровой массы. Она представляет собой порошок, который замешивают на специальном растворе. Сначала наносят первый слой фарфоровой массы – опак. Он непрозрачный, поэтому позволяет замаскировать металл. После наложения каждого слоя коронку обжигают в специальной вакуумной печи. После опака наносятся дентиновые и эмалевые массы различных цветов.
- Коронка снова передается в клинику, где происходит ее примерка без глазури.
- В лаборатории наносится последний слой – глазурь, которая придает коронке естественный блеск. Производится окончательный обжиг и шлифовка.
- Примерка коронки и ее фиксация на стоматологический цемент.
5 причин обратиться к нам
Стоматология
без боли
Врачи-
профессионалы
Современное
оборудование
Низкая стоимость
лечения
Заслуженная
репутация
Препарирование с уступом: необходимость или сверхзадача
Задача препарирования зуба с уступом или без такового стоит, прежде всего, перед стоматологами ортопедами, хотя сегодня в стоматологии активно развивается направление «дженерал дентистри», или так называемый смешанный прием.
При таком подходе границы между стоматологами-ортопедами, терапевтами и хирургами «размываются». И уже не так важно, какой специальности врач, оказывающий стоматологическую помощь, принципиален лишь выбор врача в пользу той или иной техники препарирования.
Давайте, для начала, разберемся, какой смысл вложен в создание уступа на культе препарированного зуба. Прежде всего, отметим, что уступ это не опорный элемент для коронки, хотя какую-то часть нагрузки он на себя берет. Необходимость формирования уступа продиктована, прежде всего, эстетическими и функциональными требованиями современной ортопедической стоматологии. Дело все в том, что любая искусственная коронка имеет какую-то минимальную толщину, она складывается из толщины каркаса и толщины облицовочного материала. Например, минимальная толщина каркаса из неблагородных металлов должна составлять 0,3-0,4 мм. Прибавим сюда минимально возможный слой облицовочного покрытия для получения самой скромной эстетики 0,7 мм.
Технология создания полноценного уступа сегодня проста как таблица умножения. И в данной публикации мы постараемся изложить ее в виде определенной последовательности действий врача с соответствующими пояснениями.
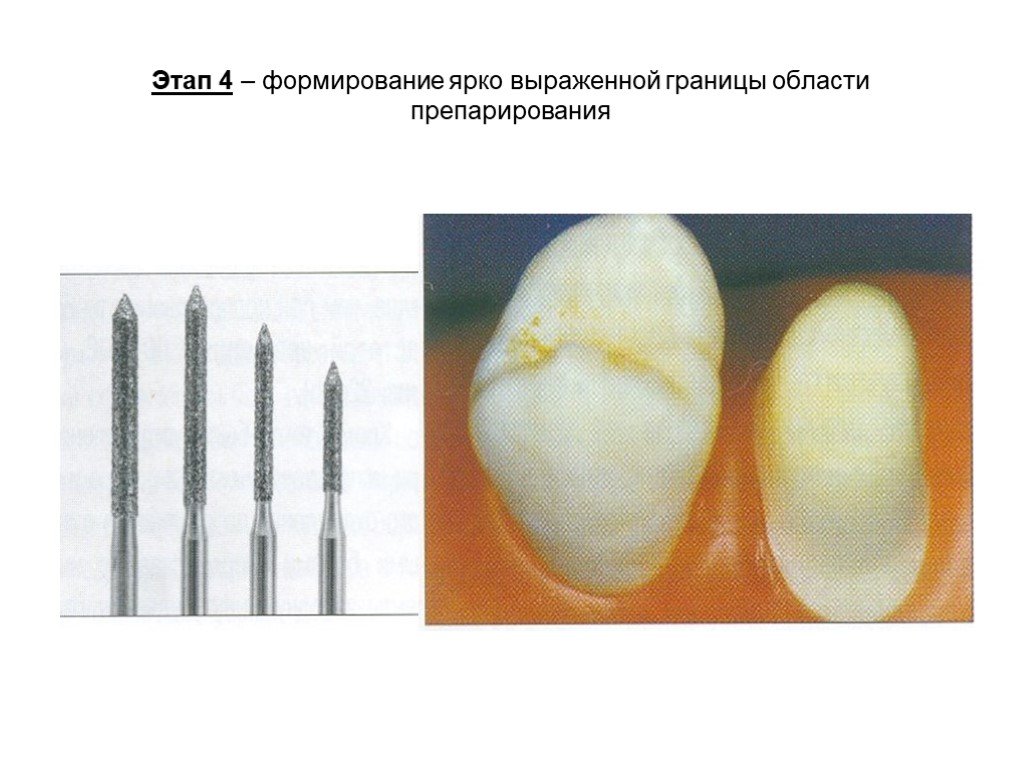
Итак, шаг №1. Создание окклюзионного разобщения. (рис. 1). Этот шаг рекомендуем выполнять алмазным бором № 909-ххх
рис. 1. Разобщение на толщину искусственной коронки
с помощью алмазного бора № 909-ххх
Шаг №2. Удаление больших объемов тканей с боковых стенок зуба. (рис. 2). Этот шаг рекомендуем производить бором с агрессивным характером сошлифовывания, идеально подходит бор серии TDA. Выполнение этого этапа, как правило, сопровождается формированием предварительного уступа выше уровня десны.
рис. 2. Удаление больших объемов тканей с боковых стенок зуба бором TDA. Одновременно формируем предварительный уступ.
Шаг №3. Формирование законченного уступа на уровне или ниже уровня десны (рис.3). Этот этап обязательно необходимо проводить твердосплавным инструментом. Конструкционной особенностью этого бора является торцевое окончание рабочей головки. У боров Great White Ultra оно увеличено в размерах и имеет большой радиус закругления, при неизменном отсутствии горизонтальных насечек на закруглении головки бора.
рис. 3. Формирование законченного уступа на уровне или ниже уровня десны.
Рис. 4. Одномоментное формирование окончательного уступа на культе зуба и финишная полировка его до глянцевой поверхности.
По данным литературы из многих форм уступов, наиболее применимы сегодня уступы в 135 градусов и в 90 градусов (чаще всего применяется его модернизированный аналог с полукруглым переходом между «стенкой и дном»).
Керметные материалы, полученные синтезом горения и пропиткой металлом (Патент)
Керметные материалы, полученные синтезом горения и пропиткой металлом (Патент) | ОСТИ.GOVперейти к основному содержанию
- Полная запись
- Другое связанное исследование
Металлокерамические композиты (керметы) изготавливаются путем сочетания синтеза самораспространяющегося высокотемпературного горения и инфильтрации расплавленного металла. Реакции твердого тела с газом, твердого тела с твердым телом и твердого тела с жидкостью в порошковой прессовке приводят к образованию пористого керамического тела, которое пропитывается расплавленным металлом для получения композитного тела с более высокой плотностью. Можно производить AlN-Al и многие другие материалы. 6 фигур.
- Изобретатели:
- Холт, Дж. Б.; Данмид, Южная Дакота; Халверсон, округ Колумбия; Лэндингем, Р.Л.
- Дата публикации:
- Идентификатор ОСТИ:
- 7277631
- Номер(а) патента:
- Номер заявки:
- PPN: США 7-283440
- Правопреемник:
- Департамент энергетики, Вашингтон, округ Колумбия (США)
- Номер контракта с Министерством энергетики:
- W-7405-ENG-48
- Тип ресурса:
- Патент
- Отношение ресурсов:
- Дата регистрации патента: 12 декабря 1988 г.
- Страна публикации:
- США
- Язык:
- Английский
- Тема:
- 36 МАТЕРИАЛОВЕДЕНИЕ; АЛЮМИНИЕВЫЕ СПЛАВЫ; ИЗГОТОВЛЕНИЕ; НИТРИДЫ АЛЮМИНИЯ; КЕРМЕТЫ; ПРОПИТКА; ЖИДКИЕ МЕТАЛЛЫ; СПЛАВЫ; СОЕДИНЕНИЯ АЛЮМИНИЯ; КОМПОЗИТНЫЕ МАТЕРИАЛЫ; ЭЛЕМЕНТЫ; ЖИДКОСТИ; ЖИДКОСТИ; МАТЕРИАЛЫ; МЕТАЛЛЫ; НИТРИДЫ; АЗОТНЫЕ СОЕДИНЕНИЯ; ПНИКТИДЫ; 360201* — Керамика, металлокерамика и огнеупоры — подготовка и изготовление
Форматы цитирования
- MLA
- АПА
- Чикаго
- БибТекс
Холт, Дж. Б., Данмид, С. Д., Халверсон, Д. С., и Ландингем, Р. Л. Металлокерамические материалы, полученные синтезом горения и пропиткой металлом .
США: Н. П., 1991.
Веб.
Копировать в буфер обмена
Холт, Дж. Б., Данмид, С. Д., Халверсон, Д. С., и Ландингем, Р. Л. Керметные материалы, полученные синтезом горения и пропиткой металлом . Соединенные Штаты.
Копировать в буфер обмена
Холт, Дж. Б., Данмид, С. Д., Халверсон, Д. С., и Лэндингем, Р. Л., 1991.
«Металлокерамические материалы, полученные синтезом горения и пропиткой металлом». Соединенные Штаты.
Копировать в буфер обмена
@статья{osti_7277631,
title = {Керметные материалы, полученные путем синтеза горения и пропитки металлом},
автор = {Холт, Дж. Б. и Данмид, С. Д., и Халверсон, Д. С., и Лэндингем, Р. Л.},
abstractNote = {Композиты из металлокерамики (керметы) изготавливаются путем сочетания самораспространяющегося синтеза высокотемпературного горения и инфильтрации расплавленного металла. Реакции твердого тела с газом, твердого тела с твердым телом и твердого тела с жидкостью в порошковой прессовке приводят к образованию пористого керамического тела, которое пропитывается расплавленным металлом для получения композитного тела с более высокой плотностью. Можно производить AlN-Al и многие другие материалы. 6 рис.},
дои = {},
URL-адрес = {https://www.osti.gov/biblio/7277631},
журнал = {},
номер =,
объем = ,
место = {США},
год = {1991},
месяц = {1}
}
Копировать в буфер обмена
Полный текст можно найти в Ведомстве США по патентам и товарным знакам.
Экспорт метаданных
Сохранить в моей библиотеке
Вы должны войти в систему или создать учетную запись, чтобы сохранять документы в своей библиотеке.
Аналогичных записей в сборниках OSTI.GOV:
- Аналогичные записи
Подготовка керметов — Соединенные Штаты Америки, представленные Соединенными Штатами
В предшествующем уровне техники использовались различные технологии для формирования керметов. Керметы, используемые в данном раскрытии, определяются как композиционные материалы, состоящие в основном из керамического вещества, но с достаточным количеством металла и с таким распределением металла, чтобы образовалась непрерывная металлическая матрица. Кермет можно представить как трехмерную структуру из металлической фольги, пространство которой заполнено керамическим материалом. Простая технология предшествующего уровня техники для формирования керметов заключается в физическом смешивании керамического порошка и порошка элементарного металла. Смесь обычно прессуется в желаемую форму, а затем уплотняется путем спекания. Другим методом является инфильтрация, при которой керамическую форму погружают в ванну с расплавленным металлом, так что поры внутри керамического изделия заполняются жидким металлом за счет капиллярного притяжения. Эти методы позволяют получать керметы, которые, как правило, способны иметь непрерывную металлическую фазу по всей структуре. Однако сохранение этой способности сильно ограничивает геометрию и нижний предел содержания металла в готовом изделии.
Другим методом формирования металлокерамики является покрытие керамических порошков металлом путем химического осаждения из паровой фазы. С помощью этого процесса отдельные порошки покрываются интересующим элементарным металлом и затем могут быть сформированы в изделие подходящей формы. Этот метод обеспечивает наличие непрерывной металлической фазы по всему изделию. Однако процесс химического осаждения из паровой фазы требует, чтобы все частицы порошка находились в очень ограниченном диапазоне размеров, чтобы процесс осаждения из паровой фазы можно было проводить в псевдоожиженном слое. Если используется смесь керамических композиций, различные порошки должны иметь одинаковую плотность для однородности псевдоожижения.
СУЩНОСТЬ ИЗОБРЕТЕНИЯ
Таким образом, целью настоящего изобретения является создание нового способа производства керметов.
Еще одной целью настоящего изобретения является создание способа производства керметов, в котором может быть обеспечена непрерывная металлическая фаза с меньшим содержанием металла, чем это требовалось в способах предшествующего уровня техники.
Еще одной целью настоящего изобретения является создание способа производства керметов, применимого к очень широкому диапазону размеров и плотностей частиц.
Эти, а также другие цели достигаются с помощью процесса, в котором образуется физическая смесь керамических частиц и соединения-предшественника элементарного металла, и соединение-предшественник разлагается в смеси с образованием элементарного металла. В результате разложения соединения-предшественника керамические частицы покрываются элементарным металлом, полученным из соединения-предшественника. Металлокерамическое изделие может быть изготовлено либо одновременно с стадией разложения, либо после нее.
ПОДРОБНОЕ ОПИСАНИЕ
В соответствии с данным изобретением было обнаружено, что металлокерамические изделия могут быть изготовлены с непрерывной металлической фазой по всему изделию при использовании лишь небольшого процентного содержания металла. Процесс осуществляется путем смешивания керамического порошка с разлагающимся соединением-предшественником элементарного металла и путем разложения соединения-предшественника в смеси. Это разложение приводит к образованию металлического покрытия на отдельных керамических зернах. По способу настоящего изобретения можно получить кермет, содержащий всего лишь 2 объемных процента металла, с непрерывной металлической фазой по всему объему кермета. Покрытие керамических частиц в результате разложения соединения-предшественника элементарного металла практически нечувствительно к размерам зерен и плотности керамических частиц.
Используемый в данном описании термин «разлагаемое соединение-предшественник элементарного металла» означает соединение, которое способно термически или химически разлагаться с образованием элементарного металла или смеси элементарных металлов или сплавов, которые находятся в несвязанном состоянии. Термически разлагаемыми соединениями, подходящими для использования в данном изобретении, являются те, которые разлагаются при умеренных температурах, т.е. ниже 1200°С, с образованием элементарного металла и газообразной фазы, которая выходит из среды кермета. К химически разлагаемым соединениям относятся соединения, которые в присутствии восстановительной или окислительной атмосферы разлагаются с образованием элементарного металла и газообразного продукта, который выходит из среды металлокерамики.
Практически любой керамический материал можно использовать для изготовления металлокерамики в соответствии со способом по данному изобретению. В частности, для формирования металлокерамики в соответствии с данным изобретением могут быть использованы следующие керамические материалы:
оксид алюминия, оксид магния, оксид кальция, оксиды железа, оксид европия, оксид циркония, стабилизированный оксид циркония, оксид тория, оксид оксиды урана, оксиды ниобия, оксид никеля, оксид бериллия, диоксид кремния, оксид тантала, оксид кобальта, оксид меди, алюмомагнезиальная шпинель, триоксид вольфрама, оксид хрома, оксид олова и оксид марганца.
Понятно, что этот список керамических материалов не предназначен для ограничения, а просто иллюстрирует керамические материалы, которые можно использовать для металлокерамики в соответствии с данным изобретением. Как правило, все керамические материалы могут быть использованы для изготовления кермета в соответствии со способом по данному изобретению.
Соединения-предшественники элементарного металла, которые термически разлагаются с образованием элементарного металла в соответствии с данным изобретением, перечислены в Таблице I ниже вместе с приблизительной температурой разложения в инертной атмосфере.
Table I |
______________________________________ |
Approximate Compound Decomposition Temperature |
______________________________________ |
TaH 0 .5 700° C UH 3 650° C ZrH 2 750°C ThH 2 850°C W(CO) 6 450°C ReCl 3 600°C |
______________________________________ |
Соединения-предшественники элементарных металлов, которые химически разлагаются для получения кермета в соответствии с данным изобретением, перечислены в Таблице II ниже вместе с предпочтительной средой и температурой разложения.
Таблица II |
______________________________________ |
Примерная температура соединения атмосферы |
______________________________________ |
PtCl 4 Hydrogen 700° C CoCl 2 Hydrogen 700° C WO 3 Hydrogen 850° C MoO 3 Hydrogen 800° C ReCl 3 Водород 500°C |
__________________________________________ |
Размер частиц исходных материалов оказывает определенное влияние на получаемый в конечном итоге кермет. Предпочтительно размер частиц оксидного керамического материала находится в диапазоне от 1 до 500 микрометров. Размер частиц материала-предшественника элементарного металла предпочтительно находится в диапазоне от 0,1 до 2 микрометров, причем большие размеры дают менее однородные покрытия. Размер частиц керамического порошка, конечно, можно варьировать для получения желаемого расстояния между металлическими слоями и желаемой степени уплотнения. Смешивание мелких и крупных частиц может быть использовано для обеспечения благоприятного баланса уплотнения и распределения металлической матрицы. Если желательно получить кермет из смешанных керамических материалов, в способе по данному изобретению можно использовать керамические частицы различной плотности без необходимости специальных мер предосторожности.
Некоторые исходные материалы преимущественно наносят на керамические порошки путем контактирования керамических порошков с раствором, содержащим исходные растворенные вещества. Предпочтительны водные растворители, но можно использовать и другие растворители, такие как спирт. В частности, хлориды можно наносить из концентрированного водного раствора. Например, таким образом можно наносить тетрахлорид платины и дихлорид кобальта. В таком случае обычно предпочтительно разлагать соединение-предшественник перед стадией уплотнения, поскольку выход летучего хлорида в виде соляной кислоты может привести к повреждению металлокерамического изделия, если будет приложено давление. Однако в других случаях, когда используется термически разлагаемое соединение, нет возражений против проведения стадии разложения, когда изделие находится в среде спекания.
Металлокерамическое изделие, изготовленное в соответствии с данным изобретением, предпочтительно изготавливают горячим прессованием. Однако спекание без приложения давления также может быть использовано для формирования металлокерамического изделия. Другие традиционные методы уплотнения, такие как нагревание путем подачи постоянного тока через изделие, могут быть использованы, если соединение-предшественник было разложено до формирования изделия.
После общего описания способа данного изобретения следующие конкретные примеры даны в качестве дополнительной помощи для его понимания. В примерах особое внимание уделяется использованию оксида европия в качестве керамического материала. Следует понимать, однако, что любой керамический материал мог быть использован для иллюстрации способа по данному изобретению и что образование керметов из оксида европия предназначено только для иллюстративных целей.
ПРИМЕР I
Моноклинный порошок полуторного оксида европия, полученный из измельченных гранул горячего прессования, нагревали в аргоне при 1800°С в течение 1 часа для обеспечения плотных отдельных частиц. Частицы имели размер в диапазоне от 50 до 200 мкМ. Порошок европия смешивали с соединениями-предшественниками путем перемешивания в стеклянной бутылке. В некоторых случаях добавляли амилацетат для облегчения прилипания и равномерного перемешивания порошков. Керметы из европия и тантала были изготовлены путем смешивания европия с гидридом тантала TaH 9.0204 0 .5, имеющие размер частиц менее трех микрометров. Смешанную порошковую смесь подвергали горячему прессованию при давлении 6000 фунтов на кв. дюйм и температуре 1430°С в вакууме внутри графического штампа. Гидрид тантала разложился, оставив в горячепрессованном образце тонкую пленку тантала. Таким образом были изготовлены керметы с содержанием тантала 2,5, 5, 10 и 20% по объему.
Кермет из европия-тантала с содержанием тантала 2,5 объемных процента был электропроводным, что указывало на наличие непрерывной фазы тантала. Были проведены дополнительные эксперименты, в которых гидрид разлагали путем нагревания рыхлой порошковой смеси 10 мас. % до 40 мас. % ТаН 0 .5 до 1000°С в вакууме перед горячим прессованием при 1430°С в течение 30 минут. Керметы, полученные таким образом, имели свойства, почти идентичные свойствам керметов, полученных разложением одновременно с этапом уплотнения горячего прессования.
ПРИМЕР II
Керметы, состоящие из европия-вольфрама, были изготовлены термическим разложением карбонила вольфрама, W(CO) 6 . Летучесть разлагаемого карбонила вольфрама соединения была проблемой и требовала быстрого нагревания до температуры выше температуры разложения. Хорошо перемешанные порошки нагревали в атмосфере аргона до 1000°С за 1,5 мин с потерей около 30% содержания вольфрама за счет улетучивания. Оставшийся вольфрам равномерно распределялся по частицам европия, за исключением центра массы, где металлическое покрытие было тоньше.
Измерения теплопроводности проводились на образцах вольфрама с содержанием европия 10 объемных процентов, полученных горячим прессованием порошка европия, покрытого указанным выше способом. Значение, полученное при комнатной температуре, составляло 6,98 Вт на метр на ° K, что составляет примерно половину ожидаемого, если бы весь присутствующий вольфрам вносил вклад в теплопроводность (т. Е. Европий не вносил вклад). Соотношение электропроводности в ледяной точке и 4,2° К указывало на то, что непрерывная фаза металлического вольфрама была достаточно чистой и на нее не оказывали неблагоприятного воздействия примеси. Следовательно, потеря теплопроводности была приписана несовершенному распределению металлической матрицы, так что часть матрицы не вносила вклад в теплопроводность.
ПРИМЕР III
Керметы из европия-вольфрама получали восстановлением триоксида вольфрама водородом. Этот метод, однако, был менее удовлетворительным, чем описанный в предыдущем примере. Водородная среда при 1000°С вызвала взаимодействие европия с вольфрамом и привело к получению кермета с большой долей вольфрама, распределенного в виде мелких частиц.
ПРИМЕР IV
Керметы из молибдена и европия получали восстановлением оксида молибдена водородом в смеси, содержащей частицы европия. После горячего прессования кермет имел равномерное распределение молибдена, но были свидетельства того, что молибден частично распределялся в европии в виде мелких частиц.
ПРИМЕР V
Керметы из оксида алюминия и вольфрама были приготовлены путем смешивания оксида алюминия и триоксида вольфрама и восстановления триоксида вольфрама водородом. Восстановление при 1000°С в водородной среде с давлением 650 мм рт.ст. привело к равномерному распределению металлических пленок на порошке оксида алюминия без распределения мелких частиц вольфрама в Al 2 O 3 .
ПРИМЕР VI
Покрытия из платины и кобальта наносили на диоксид циркония, стабилизированный 12M% иттрия, с размером частиц в диапазоне от 10 до 300 микрометров. Порошок контактировал с 35 мас.% и 25 мас.% соответственно водными растворами тетрахлорида платины и дихлорида кобальта. В каждом случае небольшое количество концентрированного водного раствора наносили на порошки оксида с помощью пипетки. Покрытые раствором частицы сушили в течение ночи при комнатной температуре, затем дополнительно сушили в течение 1 часа при 110°С. Частицы медленно нагревали до 1000°С в атмосфере водорода. Визуальное наблюдение показало, что частицы были покрыты однородным слоем. Сканирующая электронная микроскопия показала наличие металлического покрытия на отдельных частицах вместе с некоторыми перемычками. Перемычка была связана с отсутствием перемешивания частиц во время сушки раствора хлорида. Таким образом, предпочтительно перемешивать частицы, покрытые водным раствором, во время процесса сушки.
Полученные частицы с металлическим покрытием, установленные для металлографической полировки, проявляли тенденцию к выдергиванию во время полировки. Небольшие трещины между керамикой и креплением пластика появились в некоторых местах, где было снято металлическое покрытие. Типичная ширина металла и трещины составляли три микрометра, хотя отдельные участки имели толщину примерно до 12 микрометров. Слои металлической матрицы уплотнялись и упрочнялись при горячем прессовании до конечного продукта.
Таким образом, видно, что керметы, изготовленные в соответствии с данным изобретением, имеют значительно повышенные коэффициенты теплопроводности по сравнению с чисто керамическими материалами. Изделия гораздо менее хрупкие, чем керамические изделия, и поэтому не склонны к растрескиванию или сколам, как чисто оксидная керамика. Керметы, полученные способом по данному изобретению, могут выдерживать очень быстрые изменения температуры без растрескивания даже во время ядерного облучения. Способ по данному изобретению обеспечивает повышенную однородность металлической матрицы и дает непрерывную металлическую фазу с меньшим количеством металла, чем это было возможно до сих пор. Точная причина этого не совсем понятна, но считается, что она вызвана значительно усиленной диффузией металла по поверхности во время реакции разложения, которая имеет тенденцию к образованию высокооднородной металлической матрицы.
Керметы, изготовленные в соответствии со способом настоящего изобретения, имеют широкое и разнообразное применение. Керметы из оксида европия, как описано в приведенных выше примерах, чрезвычайно полезны в качестве поглотителей нейтронов в среде ядерного реактора. Керметы из оксида циркония, стабилизированного оксидом иттрия, как описано выше, чрезвычайно полезны в качестве электродного материала в процессе производства магнитогидродинамической энергии. Керметы из суперсплавов на основе диоксида циркония, легированного оксидом иттрия, и суперсплавов на основе кобальта, полученные путем горячего прессования смешанных порошков, оказались более стабильными в высокотемпературной окислительной среде, если на порошок диоксида циркония, легированного оксидом иттрия, сначала нанести тонкий слой платины или кобальта с помощью процесса, описанного выше. .
Из вышеприведенного описания становится очевидным, что в описываемом объекте могут быть сделаны многие изменения без отклонения от объема изобретения, определенного в прилагаемой формуле изобретения.